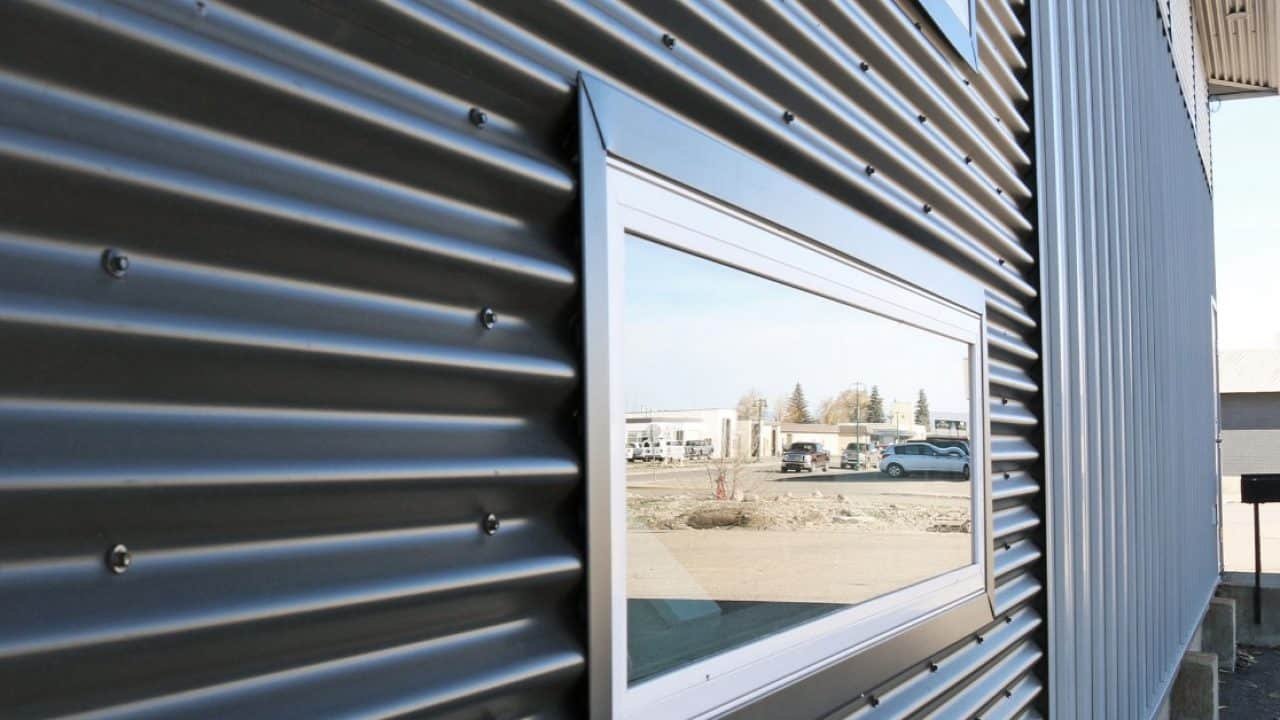
Ensuring Longevity: Best Practices in Commercial Siding Installation
Installing commercial siding on a building is a major investment. This requires careful planning and execution to ensure longevity. Proper installation techniques and regular maintenance are key to getting the most out of your commercial siding. This article outlines best practices for the installation and care of commercial siding.
Table of Contents
ToggleWhy Proper Installation Matters
The siding market in the US boasts a value of over $47 billion. With the right materials and techniques, commercial siding can last over 50 years. However, improper installation can lead to premature failure, potential safety hazards, and costly repairs down the road. Adhering to best practices protects your investment.
Siding that’s improperly installed may warp, crack, peel, and loosen over time. Gaps and imperfections allow moisture intrusion that damages the structure and interior. Loose panels become a safety hazard in high winds. Replacing warped or damaged sections is difficult and never blends perfectly.
The global siding market size was $87.26 billion in 2019 and is expected to reach $118.50 billion by 2027. Due to labor shortages in the construction industry, there’s an increased risk of errors by inexperienced installers. This makes it critical to work with reputable commercial siding contractors who follow best practices.
Investing in quality materials and ensuring proper installation upfront can result in long-term cost savings. Well-installed commercial siding can last decades with minimal repairs needed. Paying more for durable, commercial-grade materials prevents the need for replacement every 10-15 years. Proper installation prevents the high cost of correcting problems down the road.
Best Practices for Installation
Follow these guidelines for optimal commercial siding installation:
Thorough Surface Preparation
- Ensure the surface is clean, dry, and flat before installation. Remove any old paint or defective siding.
- Fill any holes or gaps with appropriate sealants. The surface must be smooth and even.
- Priming provides an extra moisture barrier and allows the siding to expand and contract. Prime the surface before siding installation.
Use Quality Materials
- Opt for thick, durable siding materials made of fiber cement, metal, brick, or stone. Avoid thin or fragile materials.
- Use siding rated for commercial use as it withstands weathering and foot traffic.
- choose nails, screws, and flashing specifically made for your siding type.
Proper Installation Techniques
- Leave a 1/4 inch gap between siding panels for expansion and contraction of materials.
- Follow the manufacturer’s instructions for spacing, nailing, and overlap of siding panels.
- Use galvanized nails long enough to penetrate the solid substrate by at least 1 inch. Nail heads should be flush with siding.
- Install metal flashing above openings and where siding meets rooflines. This prevents moisture damage.
- Caulk gaps and seams carefully to prevent water intrusion while allowing expansion and contraction of siding.
Regular Maintenance
Regular inspection and maintenance help commercial siding last longer. Undetected or unrepaired damage leads to exponential deterioration of the siding and the underlying structure.
- Inspect siding at least twice a year, in spring and fall. Walk around the entire building and look at the siding up close. Peer under overhangs and edge areas.
- Note any damaged, cracked, warped, or loose panels. Look for gaps wider than 1/4 inch. Check for rust stains, water stains, or moss growth indicating moisture issues.
- Immediately repair damaged areas and gaps with new panels or seals. Identify and correct the source of any moisture damage.
- Wash the siding gently with low-pressure water once a year. This removes dirt and contaminants. Avoid abrasive cleaners or high-pressure washing.
- Repaint faded siding every 7-10 years. Paint provides a protective barrier and restores appearance. Use high-quality exterior grade paint.
- Trim back vegetation or roof overhangs rubbing on the siding. This prevents abrasion damage and allows airflow.
Catching problems early keeps repairs manageable. Left unaddressed, water damage and deterioration escalate. Proactive maintenance leads to decades of good performance from quality commercial siding.
Common Installation Mistakes to Avoid
While using quality materials and maintenance are important, improper installation techniques are one of the main contributors to premature commercial siding failure. Be sure your siding contractor avoids these common installation mistakes:
Source: Commercial Siding Durability Report
- Not checking for plumb walls: Walls that are out of plumb can cause siding panels to buckle or leak. Always check for plumb before installation.
- Fastening incorrectly: Using the wrong type of fasteners, or spacing them improperly, leads to loose or damaged siding. Follow manufacturer specifications.
- Missing corner posts: Failing to install corner posts or treatments leaves raw edges exposed to moisture.
- Ignoring expansion gaps: All siding needs proper expansion gaps, especially metal. Not allowing room for expansion causes buckling.
- Improper spacing between panels: Too much or too little spacing between panels allows water intrusion. Follow spacing guidelines.
- Forgetting starter strips: Starter strips provide proper spacing at the bottom edge. Without them, the first course may not align properly.
- Incorrect flashing: Improper flashing at openings, penetrations, and transitions leads to leaks and hidden water damage.
- Skipping caulking: Caulking seals gaps where water can enter. Don’t skip this important step!
Following proper installation techniques is just as crucial as using quality materials. Avoiding these mistakes will lead to siding that lasts for decades.
FAQs
What is the average lifespan of commercial siding?
With proper installation and maintenance, quality commercial siding lasts 35-50 years on average. Lower quality or poorly installed siding may need replacement in 15-25 years.
How often should commercial siding be inspected?
Commercial siding should be visually inspected at least twice per year, in spring and fall. Look for damage, deterioration, loose panels, gaps, or moisture staining.
What are signs my commercial siding needs replacement?
Signs include warped, cracked, or peeling panels, rust stains, gaps wider than 1/4 inch, and persistent water stains. If more than 20% of siding is damaged, a full replacement may be needed.
Conclusion
Installing commercial siding well from the start saves money and prevents headaches later on. Follow best practices for surface prep, using quality materials, proper installation techniques, and regular maintenance.
Avoid common mistakes like neglecting flashing or using low-grade siding. With proper care, your commercial siding investment will endure for decades to come. Contact a reputable contractor if your business needs new commercial siding or repairs.